Table of Content
We do this by negotiating with factories to secure the best prices available and passing those savings onto you. No middle man costs, no retail margins, no crazy showroom overhead. Log cabin modular homes can be used as a weekend getaway, nature retreat, a hunting trip, and much more. If you’re wondering about the difference, check thiscomparison of modular homes and manufactured homes. Modular homes can be built on a basement foundation or a pier and beam system with a crawl space.

There are some prefab kit companies that will say things like two “handy” adults can build one of their prefabs in just a couple of days. But the thing to keep in mind is that the process is the same whether you are buying a tiny home or building something much larger. No matter what purpose your prefab kit home is going to serve, the land has to be ready for the build.
Prefab Homes and Modular Homes For Sale
The flooring sections have heating, electrical and plumbing connections pre-installed before they are finished with laminate, tile or hardwood. Next, the walls are constructed on a flat level surface with insulation and interior Sheetrock before being lifted by crane into position and secured to the floor sections. The interior ceilings and roof struts are next, vapor sealed and secured to each section's wall frame before being shingled.
Park model homes combine modern comfort and design with a smaller living area. The tiny house movement is quickly growing in the manufactured housing industry. Get ready to buy your manufactured or modular home with forms and checklists that cover items like expense planning and construction options. Financing your new manufactured or modular home has never been easier. We have a huge directory of trustworthy and expertly-trained lenders that specialize in manufactured housing.
Digz2Go Prefab Homes and ADUs
But with prefab materials, they’re stored safely in climate-controlled buildings, which leads to less waste from defective materials along the way. That is not to say that the quality control is necessarily lacking on site-built homes, but there have been more than a few stories about lacking quality. With prefab homes, the quality control is higher because they are being made in climate-controlled settings by the professionals who build homes regularly. If you are looking for a great value in terms of prefab kit homes, there are few better in the game than EZ Log Structures and their Florida offering is evidence of that.
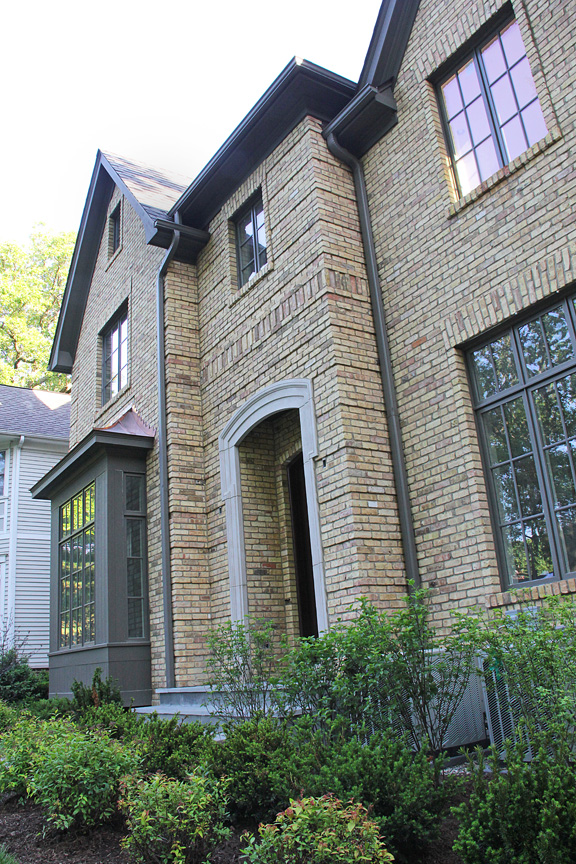
Manufactured or Mobile Homes – complete homes built in a factory and transported whole or in parts to the building site. Manufactured homes are built on a wheeled chassis frame to allow for transportation of the home. Single wides, or single section homes, are manufactured and modular homes that offer great versatility in a smaller footprint. Stop by our landmark location just off of I-25 near Johnson’s Corner to learn more about our quality, custom-built homes, and tour one of our onsite model homes today! Northstar Homes near Fort Collins is your best Custom System Home Building Solutions, proudly serving clients throughout Colorado, Nebraska & Wyoming. Additionally, Virginia Modular Homes 1st can buy building materials in bulk, passing that savings onto you, while still maintaining our high building process standards.
Featured in "Best Mobile Home Dealers" on
Finished – Typically includes land preparation, foundation, install and buttoning up, utility construction, permits, and optional additions. There are five advantages in particular that prefab home kits offer. Customizations can include plumbing and electricity, which can add to the costs, but this kit starts at just under $8,000.
With so many options, finding the right fit for your needs can become a little tougher. But with this list, you can see some of the best prefab kit homes on the market today. All of these and other advantages might make the concept of modular, prefabricated housing more real. Currently, only a small percentage of new homes are built as modular, prefab or panelized homes. However, given the numerous benefits and substantial labor savings, this might soon change.
Do you build stick-built or conventional homes as well?
Parts cut with a hand saw or a hand-held power circular saw at a job site cannot possibly be as precise as those cut with a $10,000 radial arm saw or $100,000 component cutter in a factory. Factory fastening methods are also demonstrably superior because they use pneumatic tools, which drive fasteners to precise depths – no under-driving and no shiners. The best that can be hoped for at a job site is three or four announced inspections.

Change the floorplan, select the colors and finishes, add a kitchen island or a whirlpool tub. We aim to offer you more options, more flexibility and more home for your money than anyone else in the industry. With all the building site prep work completed, the building will be delivered by trucks towing the individual sections on their permanent chassis. Modular homes are safe, permanent structures that meet building code standards and regulations like site-built homes.
A basement foundation increases the total living space and raise the property value, but are the most expensive. Modular homes come in a variety of styles, including Ranch, Cape Cod, two-story, duplex, modern, and French country. Each builder may quote different services for their base and turn-key finished homes. Always check with the builder to make sure what exactly they include in the price.
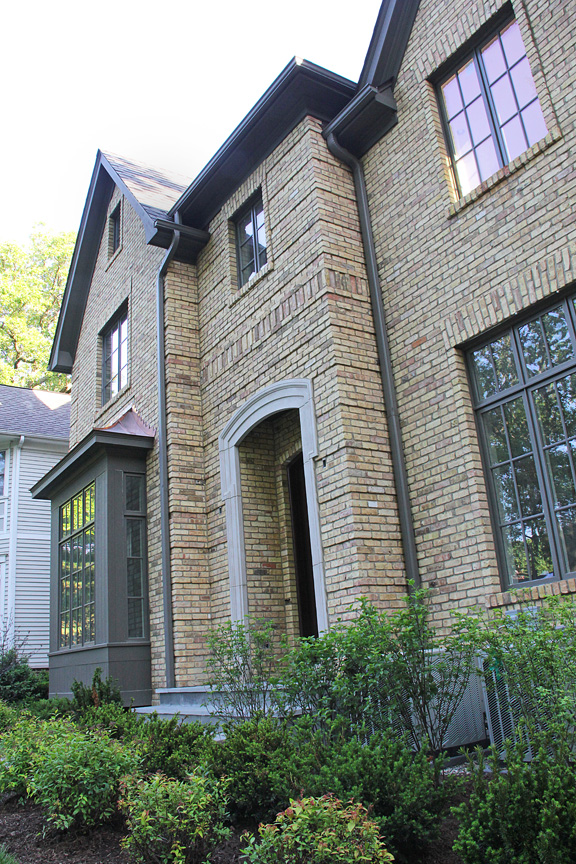
This price includes delivery, set-up, and utility connections, but excludes total site preparation fees. Kent offers more than 100 customizable floor plans ranging from 600 to 2,500 square feet. Modular log homes cost $50 to $100 per square foot on average, not including site prep, foundation, utility construction, finishings, or assembly, which adds $15 to $80 per square foot. An average 1,500 square foot log home costs $100,000 to $150,000 for just the base kit without installation.
Although many of today’s modern prefab homes focus is on high-design and super-green high-efficiency features, much of the potential of prefab housing lies in the potential for cost and time savings. Many of the initial appeals of factory-built home kits from Sears are relevant today. Cost savings, time savings, improved product quality, and consistency, as well as sustainability and environmental concerns, are driving today’s renewed interest in prefab and modular building. Regardless of whether we’re talking about factory-built, panelized, or modular homes, in-plant construction quality is invariably superior to what can be done on a job site.